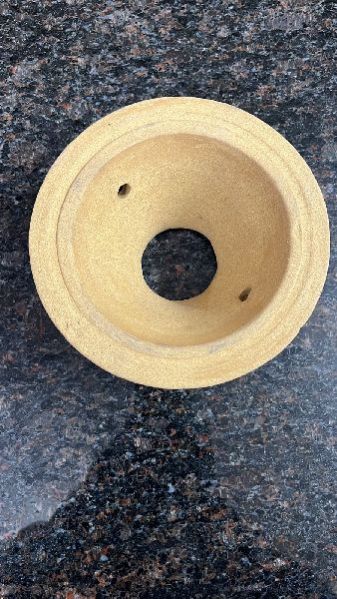
Investment casting is used for parts that require high precision, excellent surface finish and fine detail. Ceramics cup for investment casting are always in great demand. Accomplishing toughness and performance objectives requires these parts to be free from surface and internal defects. This web post clarifies the parameters the specialists centre on to realise these objectives. To begin with, although it is an overview of the investment casting process,
An IntroductiontoInvestment Casting
All casting moulds involve pouring molten metal into a mould cavity and the size and mould of the part being made. The contrast between the moulds is in how that cavity is moulded.
Investment casting begins with a wax design imitating the ultimate part. Extra wax pieces are connected to make the galleries and gates that control the metal stream into the cavity. This get-together is, at that point, secured with ceramic slurry that dries to create a problematic shell, after which the wax is softened.
Once the metal has set, the shell is broken and separated, and the metal feeder system is cut away from the cast part. From here, the part is processed for finishing and heat treatment.
Basic Casting Parameters
The two most vital parameters, in terms of their impact on the quality of cast parts, are:
• Fill rate: The speed with which the mould depth fills with metal
• Solidification rate. The speed at which the metal solidifies
The challenge is that process financial matters demand rapid filling and solidifying to maximise throughput. In any case, imperfection rates increase as process cycle time diminishes. This puts the foundry in the position of requiring to optimise both cycle time and part quality.
Overseeing Fill Rate
Amid casting, metal is poured into a container at the top of the ceramic shell. This glass is kept full, and doors near the depth control the speed of metal streams. The quick filling creates turbulence within the metal, which causes porosity and oxides. Particles washing off the ceramic shell’s inward dividers can result in incorporations.
However, if the mould is filled gradually, the metal solidifies before it is total. This leads to non-fills, particularly in thin sections, and shrinkage defects. In this way, mould designers seek an ideal gate cross-section that guarantees total filling but at the slowest speed.
Overseeing Solidification
Cementing may be a work of the cooling rate, which alludes to how rapidly heat is misplaced through the ceramic shell. The speed at which this happens decides the gem structure and, thus, the hardness and durability of the cast part. A few combinations will gradually desegregate in case it happens (where the components crystallise at distinctive temperatures).
Three components that decide the cooling rate are:
• Ceramic shell thickness
• Surface area-to-volume proportion of the part being cast: Smaller parts, or districts with a high surface area-volume proportion, relaxed quicker than locales of enormous mass
• Pouring temperature and fill speed: More sultry metal remains fluid longer, whereas slower fill speeds permit more cooling before the cavity is whole.
The cooling rate can be balanced locally by changing the thickness of the ceramic shell. In any case, part geometry frequently limits what’s conceivable. In this way, accomplishing an optimal solidification rate implies juggling fill speed, metal temperature, and shell thickness.
Other Vital Parameters
In addition to an opportunity from inner and outside defects, creating a high-quality part moreover implies assembly surface finish and geometry exactness objectives.
These are set essentially by the quality of the wax design. Any blunders or flaws in this will be transferred to the cast metal part, so it’s imperative to ensure the design is redressed. The particles’ size impacts the surface finish, beginning with a ceramic shell layer.
A Complex, Multi-Variable Issue
Maximising part quality from investment casting includes optimising the speed at which the mould cavity fills and the metal solidifies. Process financial matters push the foundry to do these rapidly, but more defects will happen if they go too quick or too moderate. Optimising the method is, in this manner, a complex issue best processed by a combination of experience and progressing modelling computer programs.